This is a new model for us, so we’re very excited. As development is needed to make and test the new foam and ensure new seat skins fit like a pair of gloves, we can only work on development jobs in the background. These jobs take us longer as we must have access and reference to the original seats. This is the only way to ensure everything is done right and well. This page will be updated as we progress.
Customer’s original tan interior, which will be changed to a black vinyl interior.
One of the issues that the customer has spotted is how saggy the backseat is when his grandchildren sit in it. Bad / worn out foam and/or potentially broken / fatigued seat springs. This will be inspected when we strip the back seat down.
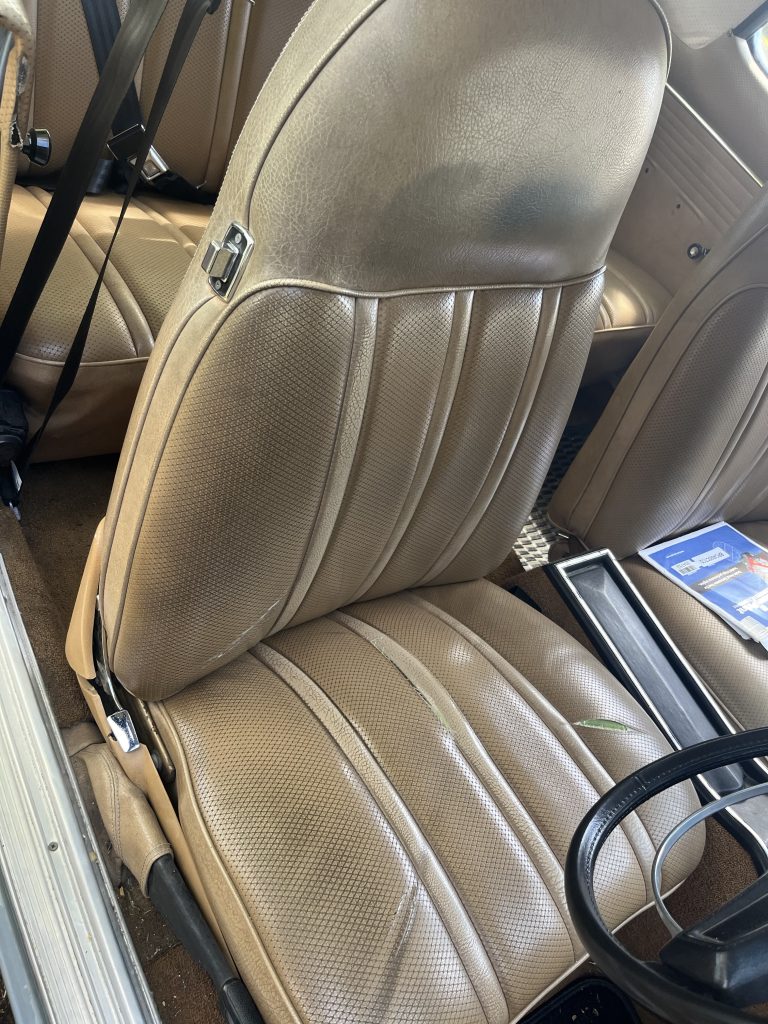
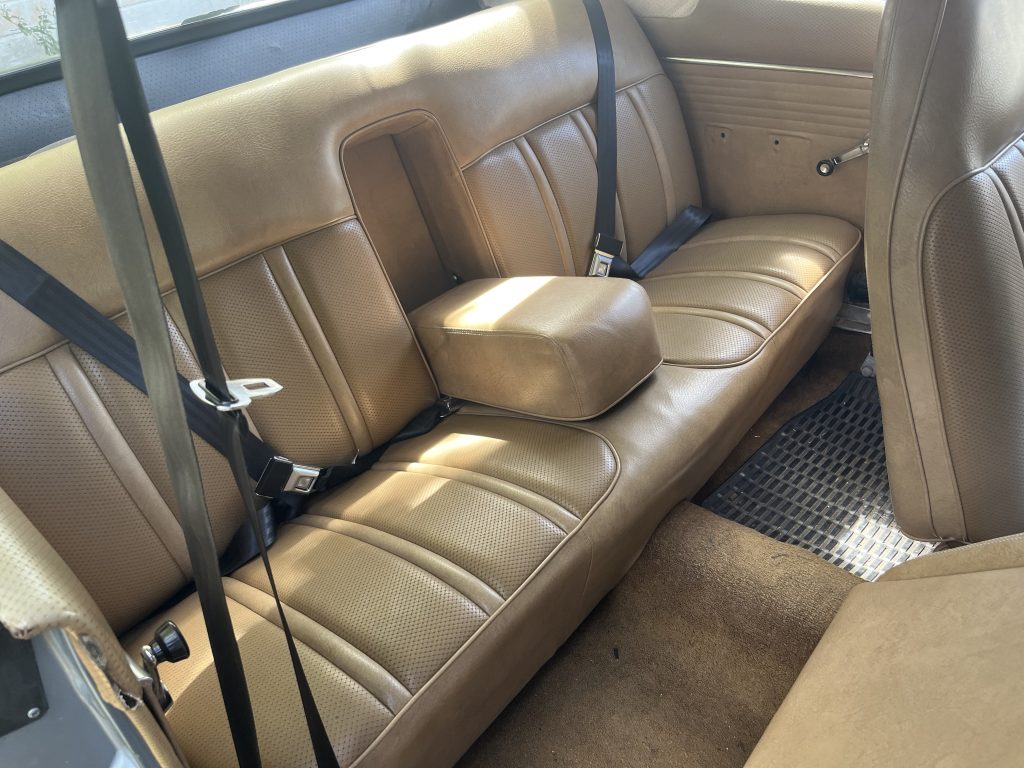
VH hardtop front seat patterns getting made:
One of the issues we have spotted in the front seats is that we can feel the metal of the seat. This indicates that over time, the foam and skin have shrunk so much so that the foam is essentially crêpe. The seat skin hugs and wraps around the seat as if it were fitted over bare frame, without much in the way of cushioning / padding. What should have been 25mm thick foam when new, for example, would look about 10mm thick by the time we strip the seat down and inspect the foam. This is why we find it extremely inaccurate and pointless to copy from shrunk vinyl skins. Fitting that back onto seats means you will either have to use old foam, or deliberately use a smaller / slimmer foam kit.
Inspections of the factory foam show what’s lacking:
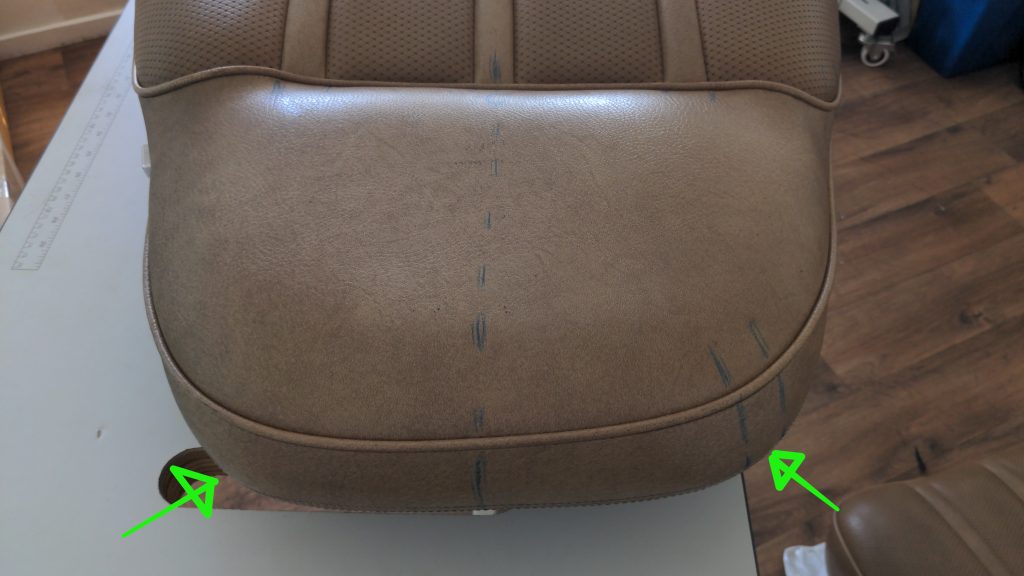
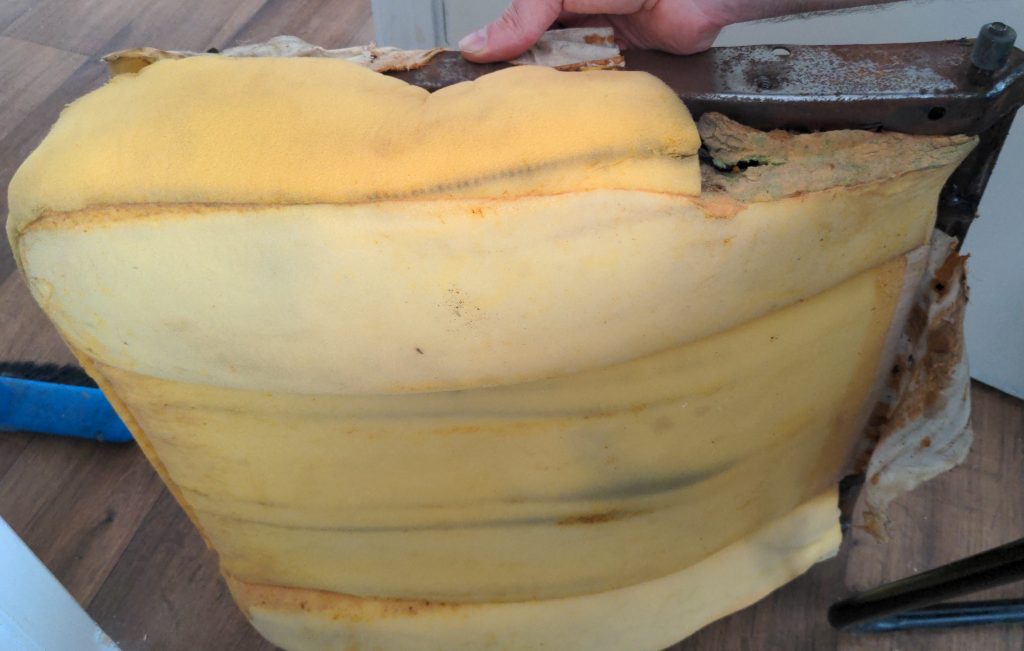
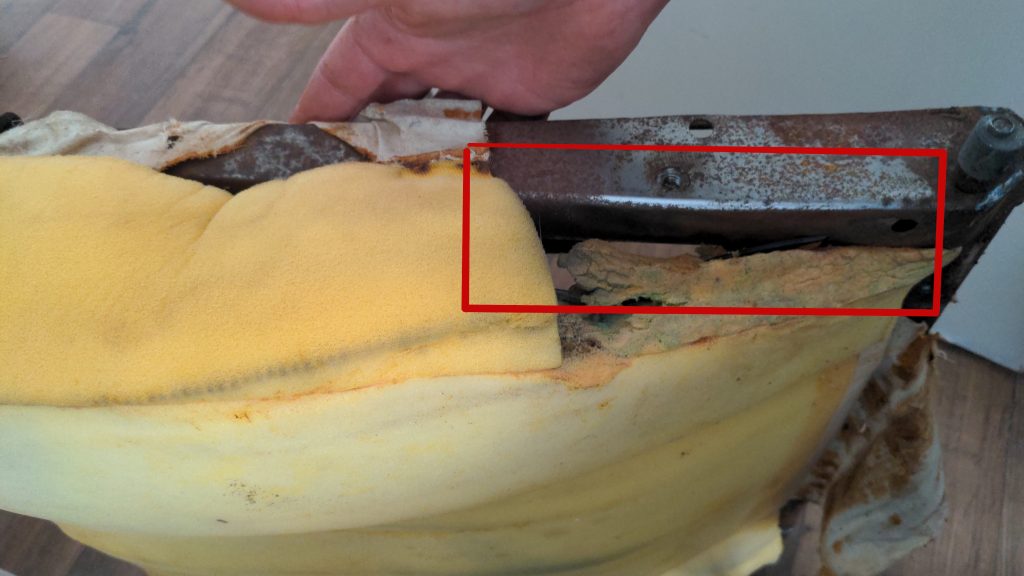
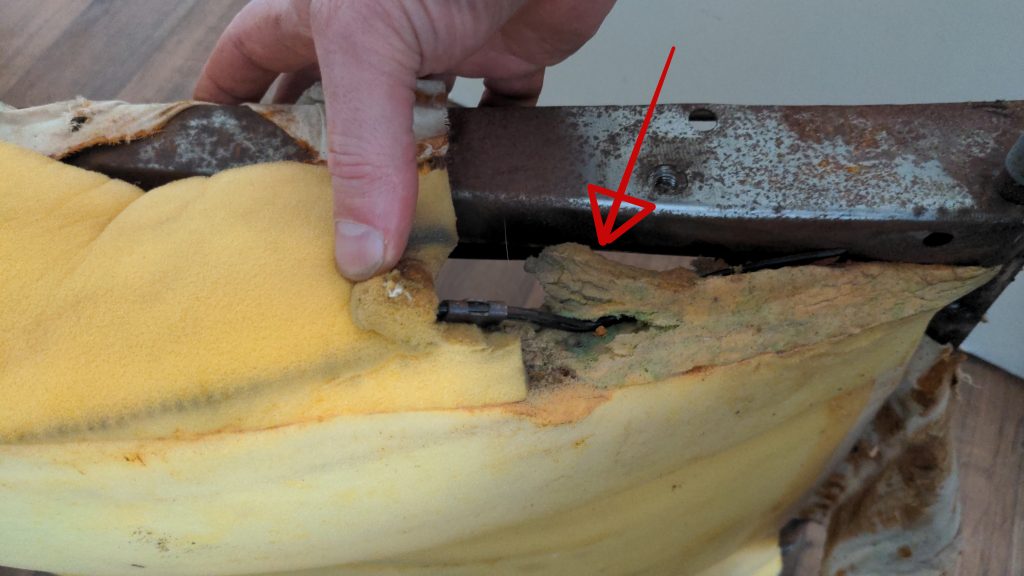
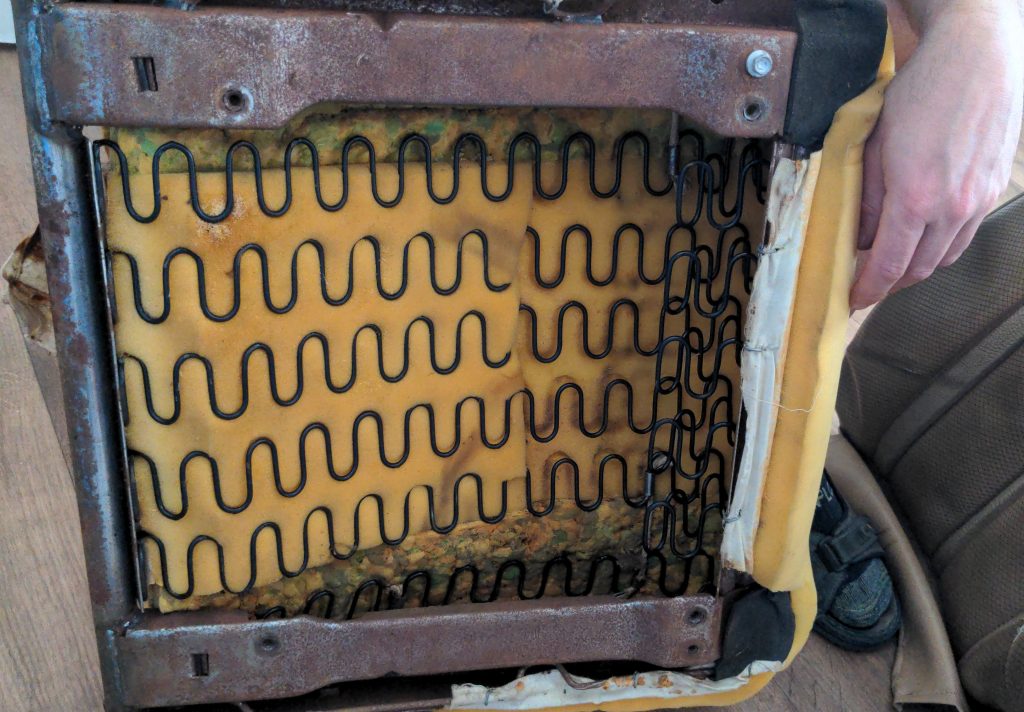
Door Cards:
Meanwhile, we’ll be sourcing the backing panels for these door cards. The door trims will be recreated using a sewing machine. So the heat pressed stitches from factory will be real stitches. Door trim backing panels will also get test fitted to the actual doors before the door trims get made.
To be continued…